We’ve made tremendous progress on this project since our last update and we’re excited to share with you. Follow along as we build Sarasota’s luxury homes.
Our last update was at roof dry in and there has been huge progress on this project since then. Interior framing is about 90% complete, mechanical rough ins have just started and window installation is about 20%. Follow along as we build Sarasota’s luxury homes.
Framing
Once the roof is dried in its time to move to the interior and start with framing interior partitions and ceiling details. A good framing crew and high quality material are a must and in both of these categories we use the best. Some of our framing crews have worked with us for decades. Framing perfection is important for many different reasons the most obvious of which is the quality of the finished walls. Imperfections in framing only become more obvious as finishes are applied, drywall does not hide poor framing quality. “Start Right Stay Right”
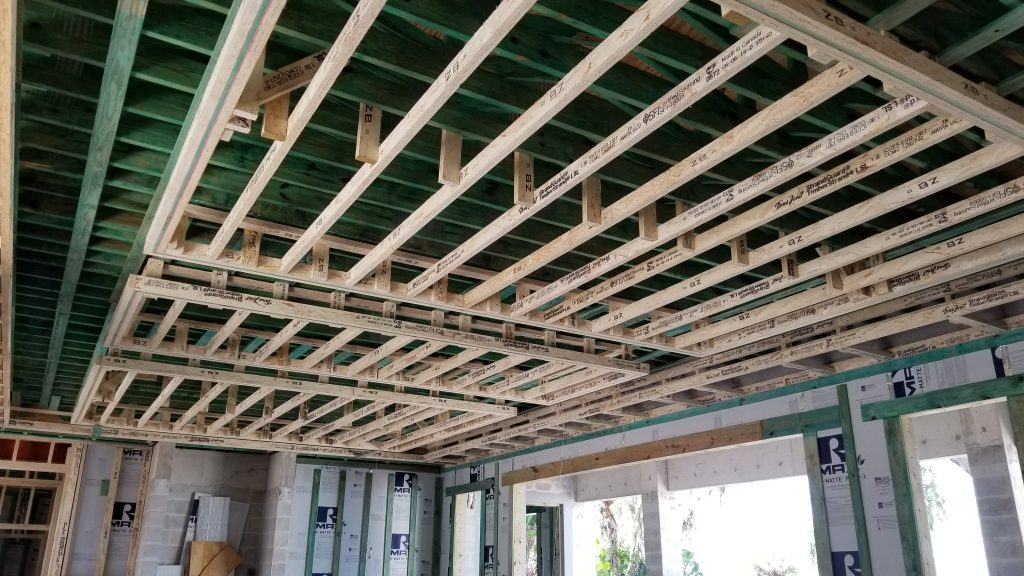
The cieling detail here is in the great room. High tech tools and proven techniques are used to achieve a perfectly level, plum and square
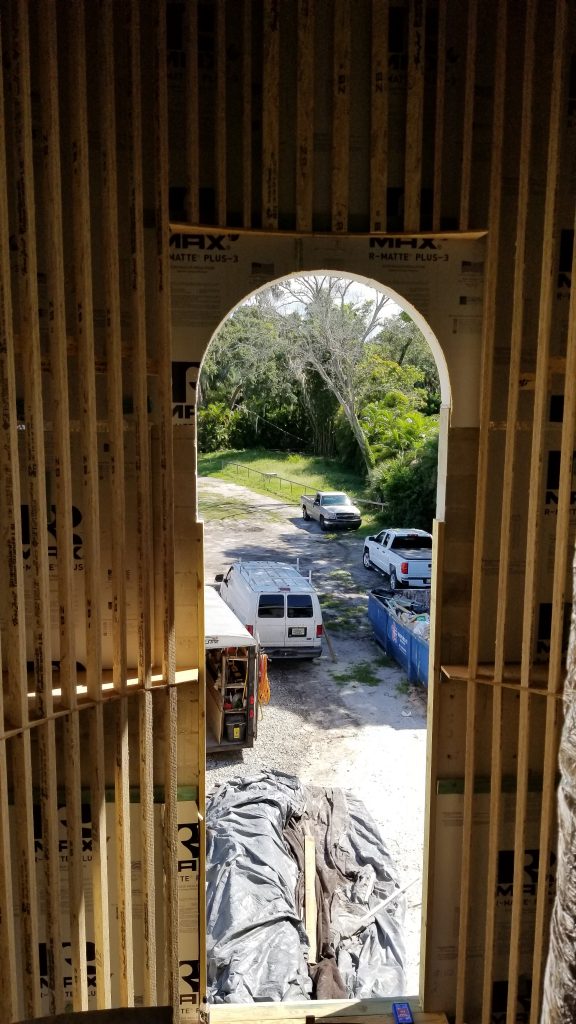
This is a radius wall at the stairwell. The wall goes up thirty feet and has to be perfectly plum. Craftsmanship and material selection are especially critical here.
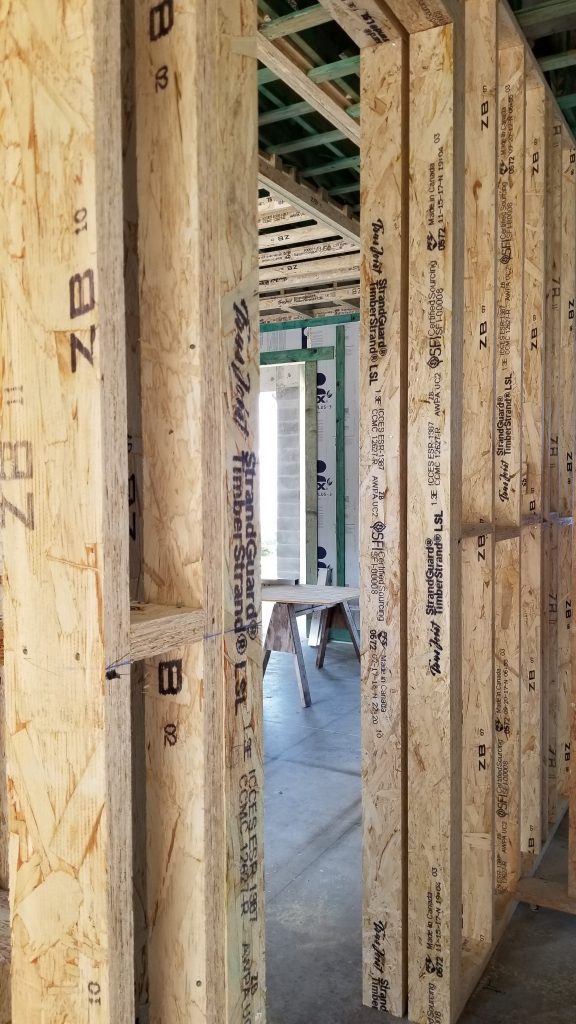
If you are interested please set up a time to learn about what we do above and beyond the standard in the construction industry. We can promise it will be time well spent
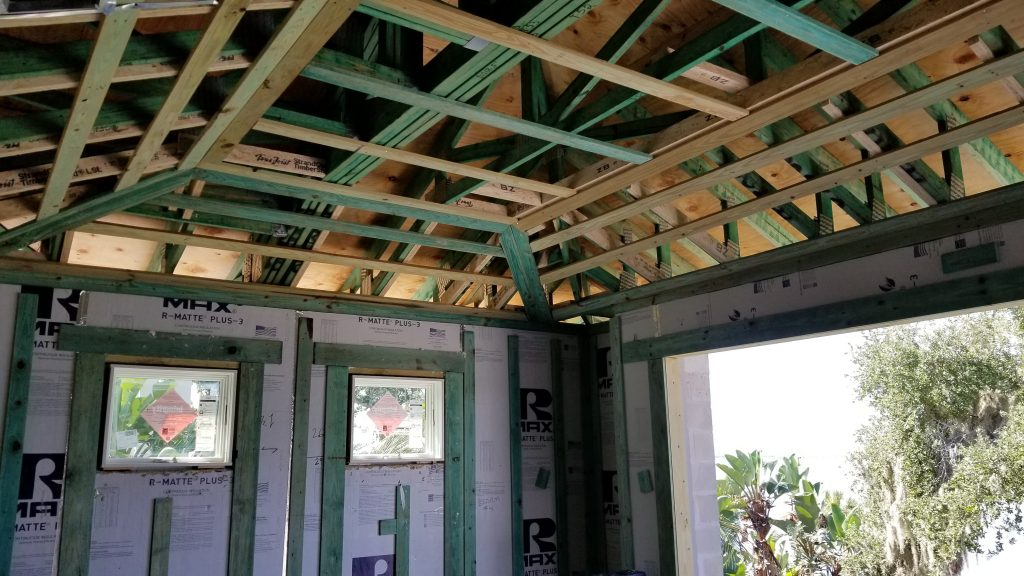
We incorporate some of our ceiling details into the truss design
Pool
The pool on this home is unique in that it abuts right to the structure of the house. This is not something that is difficult to achieve but it does take some coordination between the engineer, architect and our team. The end result is a very dramatic resort like feel. The strucutre of the pool is typically installed early in the project as there is quite a bit of digging and access becomes restricted as the project progresses. The pipes visible in the bottom of the pool are an in floor cleaning system.

Now that the steel and form board are in place the pool is ready to be “shot”
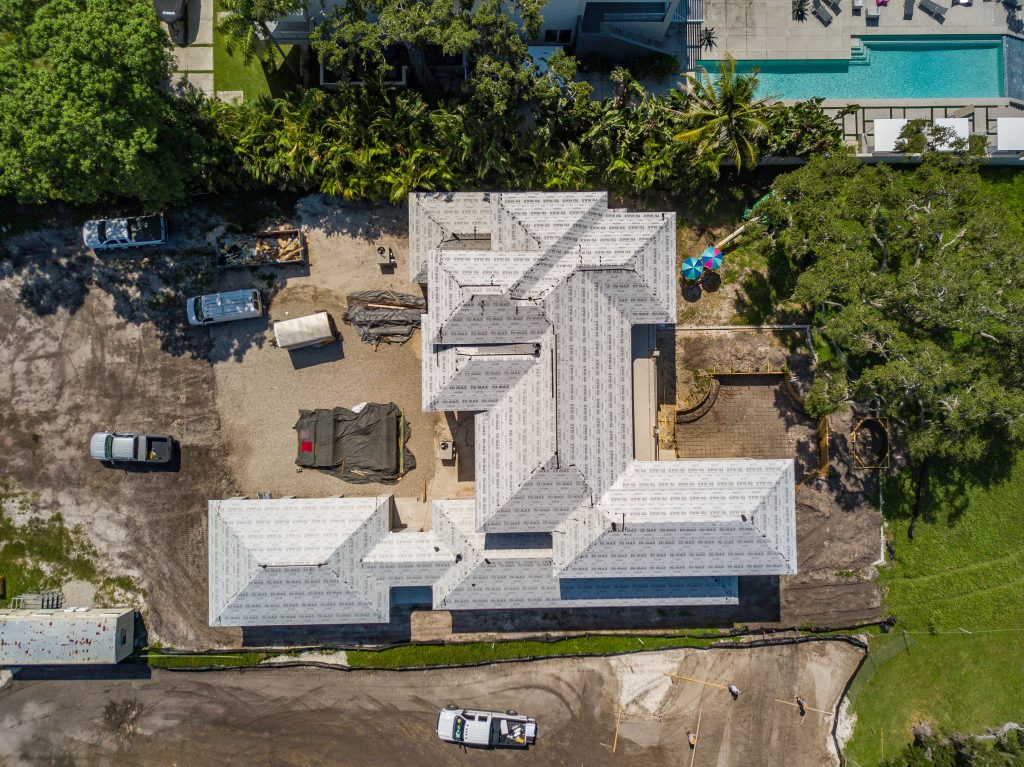
An overhead view o the pool
Windows
Once the roof is dried in windows can be installed. These windows were ordered prior to starting with masonry work. The sizes of the masonry openings need to be very exact because the windows need to fit very tightly to pass inspection so there is not much margin for error. Once the masonry opening is created it is waterproofed and a “buck” is installed with a bead of waterproof caulk on the back, it is fastened in place with tapcons. Once this is installed the window can be placed in the opening. Its critical these are installed level and that the extension jambs plane out with the future drywall finish.
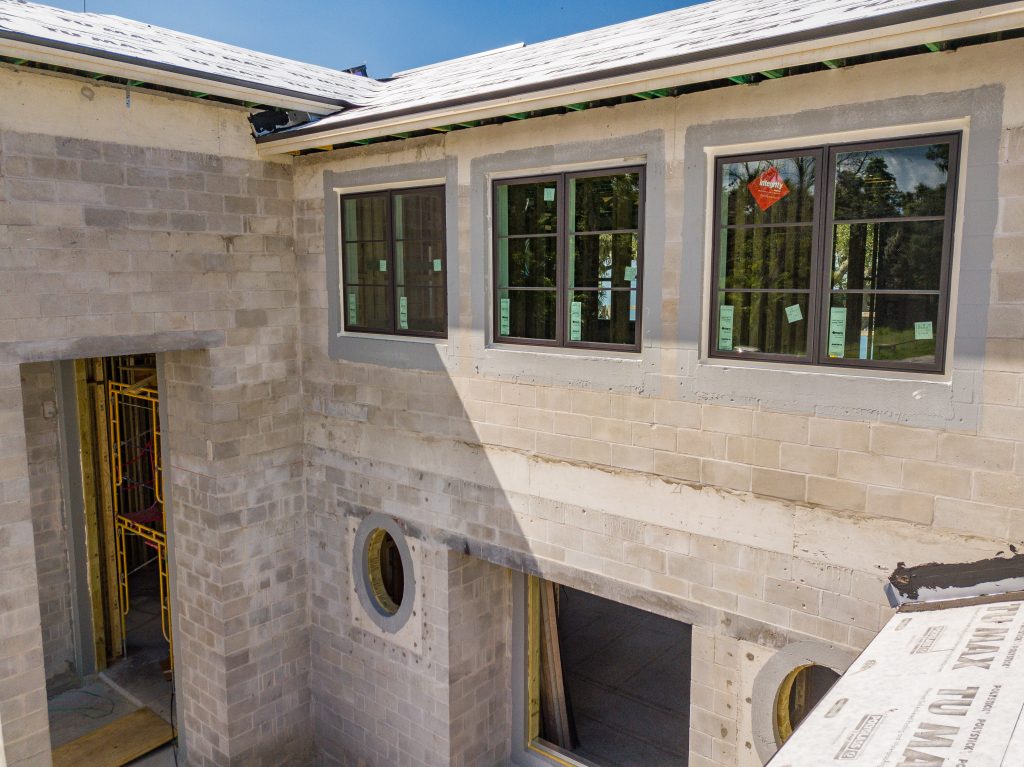
Windows installed at the second level. The masonry waterproofing is visible in grey around the windows
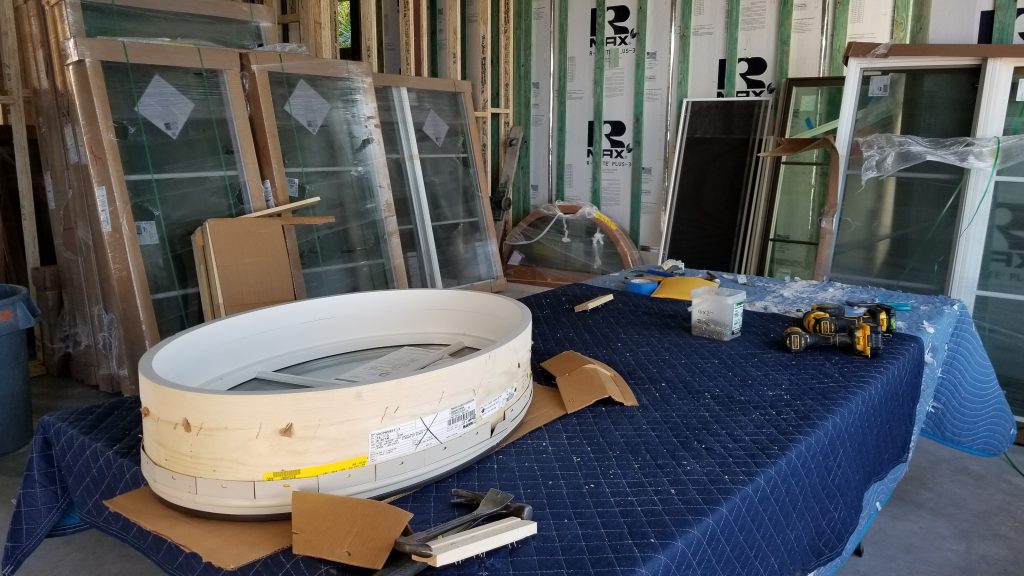
A window installer preps a radius window for installation
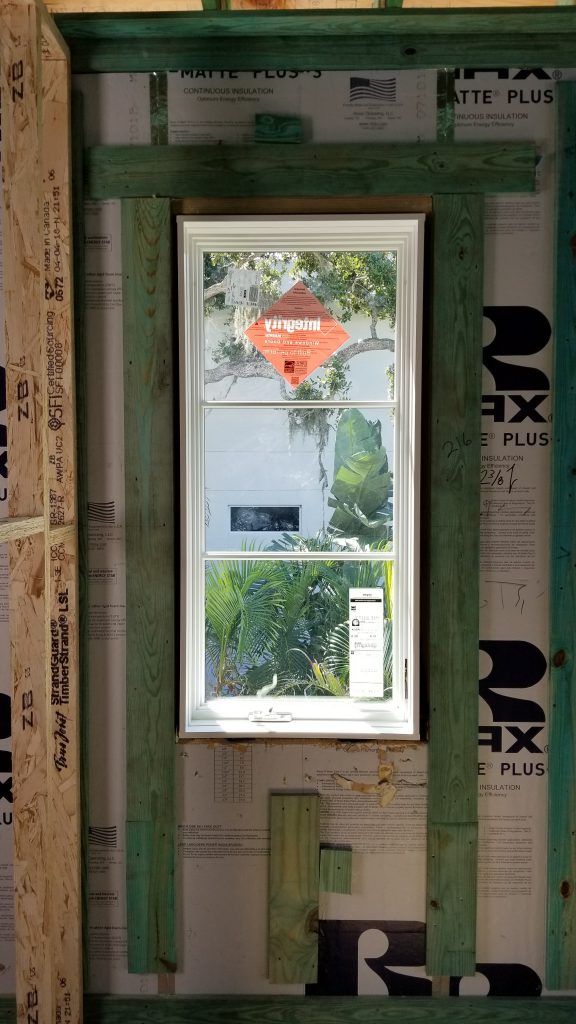
An interior view of an installed window. The extension jam needs to set in from the firing stris 5/8 of an inch to plane out with the drywall at every point around the window.
Rough Ins
Rough ins have to do with the electrical, plumbing, gas, low voltage and HVAC systems in the home. Anything that goes in an attic system floor system or wall is installed during the rough in stage. Rough ins are examined early to be sure we have a clear path to run things like HVAC and plumbing.
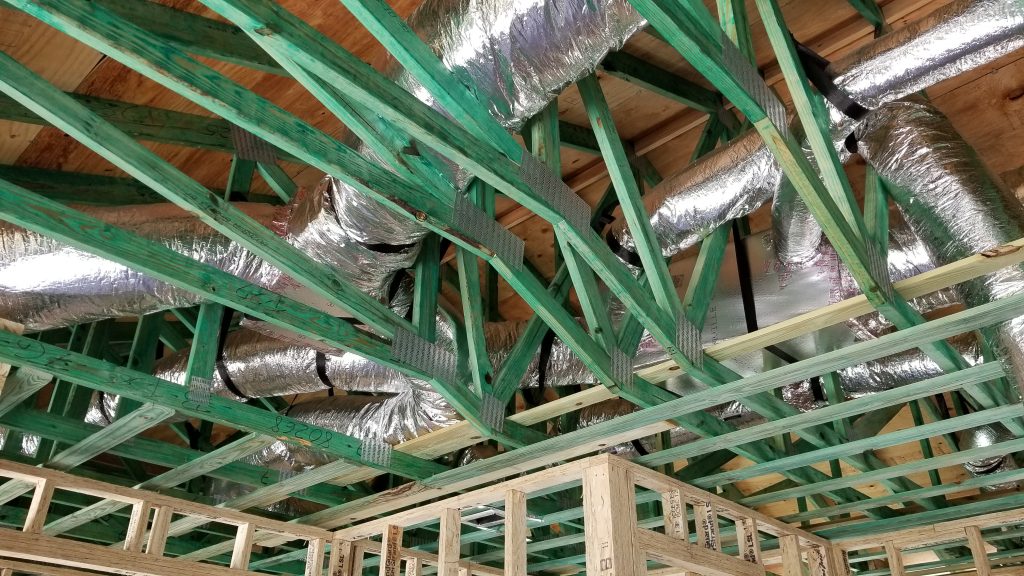
HVAC Rough Ins